Understanding Powder Coating: A Practical Guide
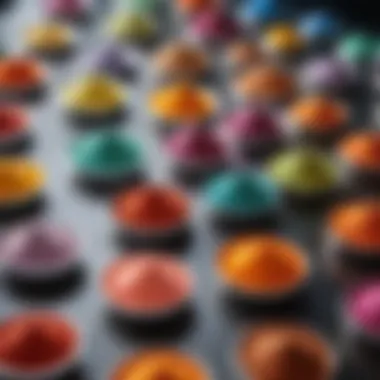
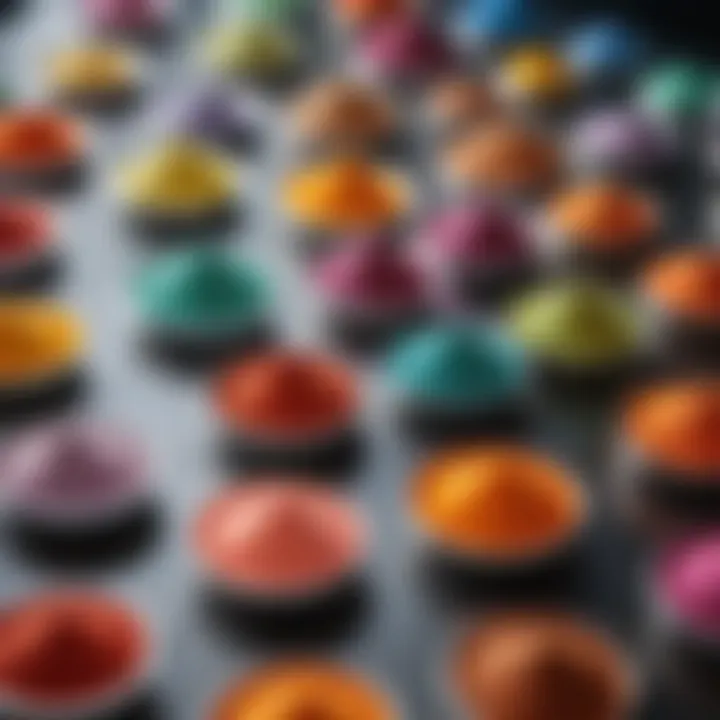
Intro
Powder coating is a process that has gained significant traction in various industries, due to its durability and aesthetic appeal. This technique involves applying a dry powder to a substrate, which is then cured under heat to form a hard finish. Used widely in automotive, furniture, and architectural applications, powder coating offers both protective and decorative qualities. This guide will demystify the principles and practices of powder coating, making it accessible for enthusiasts and professionals alike.
By understanding the nuances of powder coating, readers will be better equipped to make informed decisions, whether they are looking to enhance the visual appeal of an object or seeking protection against the elements. We will delve into the advantages, common applications, and practical tips for executing a successful powder coating project.
Prolusion to Powder Coating
Powder coating is a critical method in the field of surface finishing, known for offering both aesthetic and functional advantages. It involves applying a dry powder to a surface, which is then cured under heat to form a durable finish. The significance of powder coating lies in its ability to enhance the appearance and longevity of various materials. This introduction aims to outline fundamental concepts related to powder coating and its far-reaching benefits.
What is Powder Coating?
Powder coating represents a process where finely ground particles of pigment and resin are electrostatically charged, allowing them to adhere to surfaces. Once applied, these particles are subjected to a curing process, typically involving high temperatures. During this phase, the powder melts and chemically fuses into a robust polymer coating.
Some key characteristics of powder coating include:
- Durability: The finish is significantly more resistant to chipping, scratching, and fading compared to traditional paint.
- Environmentally Friendly: Powder coating produces minimal volatile organic compounds (VOCs), making it a healthier option.
- Variety: It offers numerous textures, colors, and finishes that can suit varied design preferences.
Understanding what powder coating is sets the stage for evaluating its historical context and modern applications.
Brief History of Powder Coating
The origins of powder coating can be traced back to the late 1940s. Early developments were focused on improving the aesthetic appeal and durability of coated surfaces. Initially, it gained traction in the automotive sector. With advancements in technology, powder coating expanded its reach to numerous industries including architecture and furniture.
The process underwent significant improvements by the 1960s with the introduction of electrostatic spraying techniques. This innovation improved application efficiency and quality of the finish. Today, powder coating has evolved into a sophisticated industry, benefitting from ongoing research into new materials and procedures.
"Powder coating not only enhances aesthetics but also adds protective qualities to surfaces, making it a preferred choice across various industries."
The Powder Coating Process
The powder coating process is a pivotal element of the overall powder coating technique. It seamlessly transforms raw materials into a finished product that is both functional and visually appealing. Understanding this process is crucial for both enthusiasts and professionals. It helps to appreciate how each step contributes to the quality, durability, and aesthetic of the final coated surface.
Preparation of Surfaces
The first step in powder coating is surface preparation. Proper surface prep ensures that the powder adheres well and creates a smooth, even finish. Dirty, rusty, or uneven surfaces can lead to various defects in the powder coating, reducing the lifespan of the coating.
Common surface preparation methods include:
- Cleaning: This involves removing dirt, grease, and old paint. Common cleaning agents are solvents or alkaline cleaners.
- Mechanical Abrasion: Sandblasting or grinding can be used to achieve a rougher surface profile. This helps the powder bond effectively.
- Phosphate Treatment: Often used in industrial settings, this creates a corrosion-resistant layer and improves adhesion.
Getting this step right can substantially enhance the overall quality of the coating. The importance of meticulous preparation cannot be overstated as it sets the foundation for a successful coat.
Application Techniques
After the surfaces are well-prepared, the next stage is the application of the powder. There are several methods to apply powder coatings, each suitable for different scenarios.
- Electrostatic Spraying: This is the most common application technique. It uses an electrostatic charge to attract powder to the grounded surface, ensuring an even distribution.
- Fluidized Bed Coating: This technique involves pre-heating the parts and dipping them into fluidized powder. The heat causes the powder to melt and adhere. Ideal for complex shapes, it creates a thick coating.
- Tumbling: A less common method, tumbling uses a rotating drum to coat small parts. This method is efficient for producing more uniform coverage on small, intricate items.
Each method has its unique advantages and ideal use cases. Choosing the right technique affects not just the finish, but also the efficiency and cost of the operation.
Curing Process
Curing is the final step in the powder coating process and is critical for achieving a durable finish. During curing, the coated item is subjected to heat, which causes the powder particles to melt and flow together. This chemical reaction transforms the powder into a solid, continuous film.
Typical curing involves:
- Temperature: Most powder coatings cure at temperatures between 350°F to 400°F (about 180°C to 200°C).
- Time: The curing time can vary based on the powder type and thickness of the coating. Usually, it ranges from 10 to 30 minutes.
The effectiveness of this step impacts the overall durability of the coating. Proper curing ensures the resistance to scratches, chemicals, and environmental factors such as corrosion.
In summary, the powder coating process is an amalgamation of preparation, application, and curing, each step paramount in ensuring the integrity of the finish.
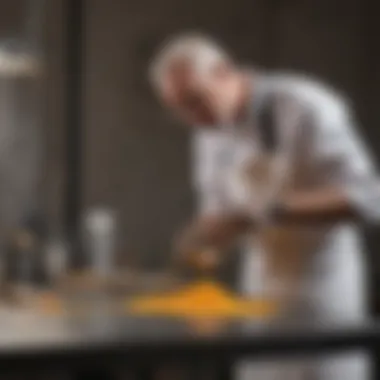
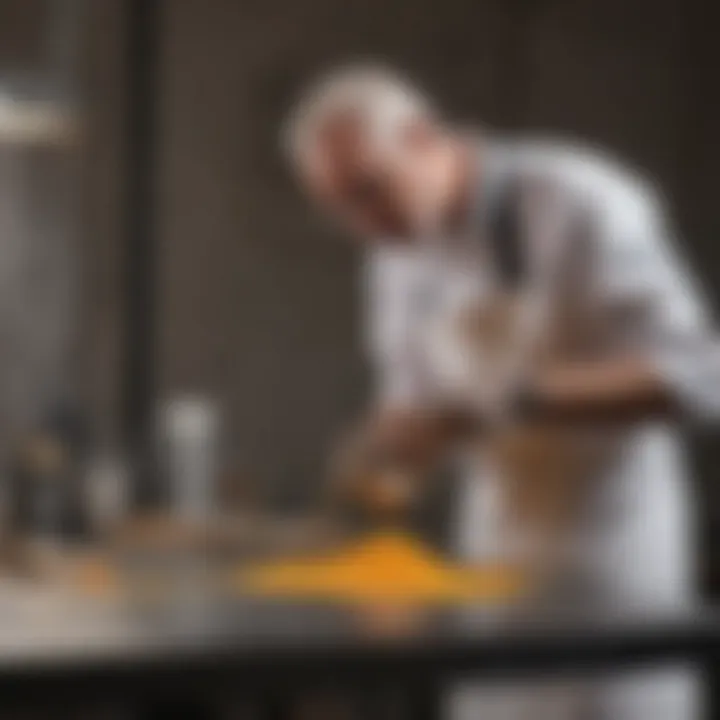
Understanding these processes is essential for anyone interested in powder coating, whether for DIY projects or more extensive industrial applications.
Materials Used in Powder Coating
The materials utilized in the powder coating process play a significant role in determining both the aesthetic and functional outcomes of coated products. Understanding these materials is essential for anyone looking to achieve high-quality results. Choosing the right type of powder, along with considering its properties, can lead to successful applications in various industries.
Types of Powder Coatings
Powder coatings generally fall into two main categories: thermosetting and thermoplastic powders. Thermosetting powders undergo a chemical change when cured, which makes them more durable and resistant to chipping, fading, and scratching. They are ideal for applications where tough finishes are needed. On the other hand, thermoplastic powders can be remelted and reshaped, making them suitable for uses where flexibility is important.
- Pros of Thermosetting Powders: High durability, excellent resistance to harsh conditions.
- Cons of Thermosetting Powders: Irreversible once cured.
- Pros of Thermoplastic Powders: Can be reused and reshaped, good impact resistance.
- Cons of Thermoplastic Powders: Generally less chemical resistant than thermosetting.
Choosing the Right Powder
Selecting the right powder coating is crucial. There are several factors to consider to ensure optimal results.
Color Options
Color options significantly influence the overall appearance of the final product. The availability of various colors allows for creativity and personalization. Moreover, colored powders can match specific branding requirements or design preferences. The key characteristic of color options lies in their versatility. Some colors can reflect heat, which may benefit applications exposed to high temperatures. However, darker colors may hide imperfections better than lighter tones. It's essential to note that color fades over time, depending on environmental exposure.
Finish Types
The finish type is another critical consideration. Powder coatings can have different surface finishes, such as gloss, satin, and matte. Each finish provides a distinct look and feel. For instance, a glossy finish reflects more light, contributing to a vibrant appearance. On the contrary, a matte finish can help conceal surface imperfections and gives a modern aesthetic. Finish types can affect not only the visual appeal but also the performance characteristics of the coated surface, particularly in terms of maintenance and cleaning.
Durability Features
Durability features of the powder coating material are vital for longevity and protection. Key characteristics include resistance to scratches, solvents, and corrosion. Thermosetting powders, especially, provide superior durability, making them ideal for industrial applications. This characteristic allows them to maintain their integrity even in challenging environments. The unique feature of durability in powder coatings lends itself to cost savings over time, as fewer repairs and replacements are needed. However, it is essential to assess whether the added durability aligns with the specific usage requirements of each project.
"Choosing the right materials for powder coating is not just about aesthetics but also about ensuring performance under real-life conditions."
Evaluating these aspects—color options, finish types, and durability features—will greatly inform the success of the powder coating application, whether for DIY projects or professional deployment.
Advantages of Powder Coating
The advantages of powder coating are indeed significant in various applications. This section examines key elements of powder coating benefits, showcasing why both DIY enthusiasts and professionals should consider this method. The advantages include environmental sustainability, economic savings, and notable durability.
Environmental Benefits
One of the most compelling advantages of powder coating is its environmental impact. The process emits fewer volatile organic compounds (VOCs) compared to traditional liquid coatings. This reduction is advantageous for air quality and ecosystem health. Moreover, any excess powder can be reclaimed and reused, which reduces waste and promotes efficient resource use. By choosing powder coating, individuals and industries can contribute to a greener future and align with environmentally friendly practices.
Cost-Effectiveness
Cost-effectiveness is a critical consideration for anyone looking to coat materials. The initial investment in powder coating equipment may be higher, but savings occur over time. Powder coating generally covers more surface area per pound than liquid coatings. This can lead to reduced material costs and less frequent purchases. Additionally, the durability of powder coatings means that repairs and maintenance costs are lower in the long run, achieving a beneficial balance between upfront costs and long-term expenditures.
Durability and Resistance
Durability is another primary advantage of powder coating. Its robustness extends the lifespan of coated items, even in tough environments. Below are specifics on two key types of resistance provided by powder coatings:
Corrosion Resistance
Corrosion resistance stands out as a defining characteristic of powder coatings. Items coated with this method can withstand exposure to moisture and harsh chemicals without deteriorating. This feature is especially beneficial for metal products subjected to rain, humidity, or industrial settings. Maintaining the structural integrity of metals over time can prevent costly replacements and enhance the overall value of these items. This resilience makes powder coating a preferred choice for many industries.
Chemical Resistance
Chemical resistance is equally crucial for applications in environments where exposure to solvents and chemicals is common. Powder coatings are formulated to resist various harsh substances. This not only protects the substrate beneath but also maintains the aesthetic qualities of the finished surface. This advantage saves time and resources by reducing the need for frequent re-coating or maintenance, thus proving to be a sound investment in the long term.
"Powder coating is a method of applying a protective finish that offers high durability and less environmental impact than traditional coatings."
In summary, the advantages of powder coating include a favorable environmental footprint, cost benefits over time, and a high level of durability. Emphasizing these benefits can guide consumers and industry professionals in making informed choices regarding their coating needs.
Applications of Powder Coating
The applications of powder coating are vast, making it an indispensable process across various industries. Its versatility is a result of the protective and aesthetic advantages it delivers. With numerous sectors benefiting, understanding these applications provides insight into its relevance and functionality. This section discusses how powder coating is utilized industrially, within the automotive industry, and in consumer goods. It is important to grasp these diverse applications to appreciate the practical outcomes and efficiencies achieved through powder coating.
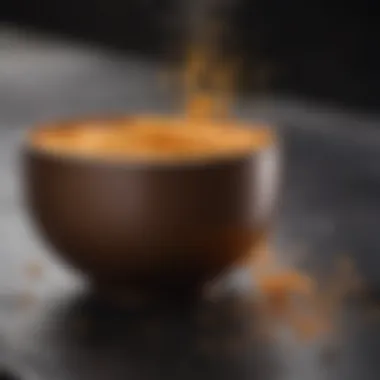
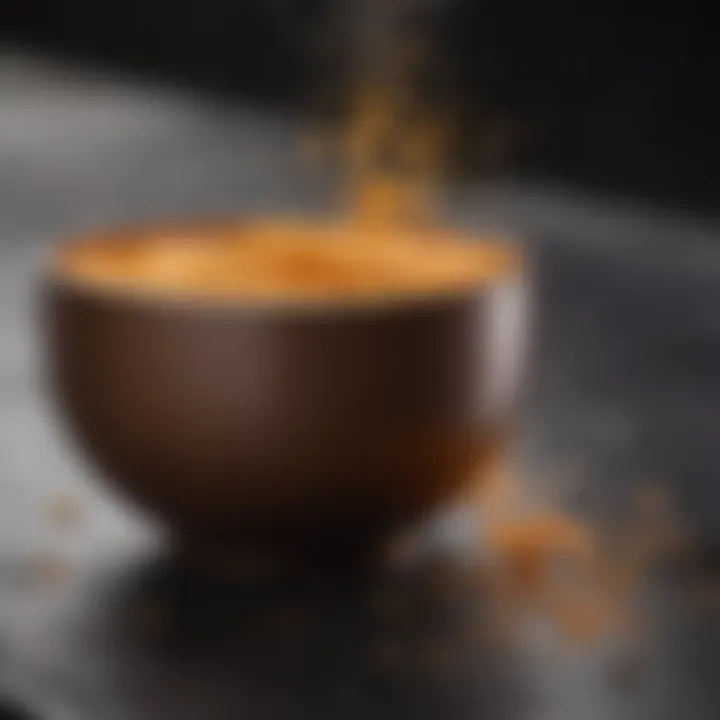
Industrial Applications
In industrial settings, powder coating offers exceptional durability and resistance to various environmental factors. It is commonly used to coat metal components in machinery and equipment, ensuring longevity and minimal maintenance. The robust finish protects against corrosion, UV exposure, and impacts, which is crucial for industries like manufacturing and construction.
Key benefits of industrial applications include:
- Enhanced durability: Powder coated materials exhibit superior wear resistance.
- Environmental protection: The finish acts as a barrier against hazardous substances.
- Cost-effective maintenance: The longer lifespan reduces replacement costs.
Products such as racks, frames, and bulk containers, often undergo powder coating to optimize performance and extend usability. The ease of applying various colors also allows companies to maintain brand consistency through aesthetic appeal.
Automotive Industry Usage
The automotive sector extensively employs powder coating for both appearance and performance. Vehicle manufacturers use powder coating on frames, body parts, and wheels to enhance durability and provide a uniform finish. The application not only makes parts resistant to chipping and scratching but also enables intricate designs and colors. This is vital since consumer expectations for automotive aesthetics are high.
Notable advantages in automotive applications include:
- Improved corrosion resistance: Essential in prolonging the vehicle's life in different climates.
- Weight efficiency: The coating process adds less weight compared to traditional liquid coatings.
- Customizable finishes: Provides diverse options for owners' preferences.
Brands often rely on powder coating as a reliable finishing option, creating a unique blend of functionality and beauty.
Consumer Goods
In the realm of consumer goods, powder coating plays a pivotal role in enhancing product appeal and functionality. Many household items, such as furniture, electrical appliances, and outdoor equipment are powder coated to improve their aesthetic and physical properties. The process allows for vibrant colors and textures that attract buyers, enhancing appeal in retail settings.
Here are aspects that highlight its significance in consumer goods:
- Aesthetic enhancement: Products gain a professional finish that attracts customers.
- Durability: Furnishings and appliances can withstand daily wear and tear.
- Safety: Non-toxic materials used in powder coating make finished goods safer for consumers.
In summary, powder coating is vital across various sectors, enhancing durability, aesthetics, and safety. Its applications range from industrial machinery to consumer products, and this multifaceted utility solidifies its standing as a preferred finishing method.
DIY Powder Coating
Engaging in DIY powder coating offers numerous benefits for both aesthetics and functionality, making it a significant topic within this article. The process allows individuals to coat various materials, achieving a durable and visually appealing finish at home. This section will detail essential tools, equipment, and a practical guide to help novices successfully navigate the world of DIY powder coating.
Essential Tools and Equipment
Before starting a DIY powder coating project, having the right tools and equipment is crucial. Here are some of the key items needed:
- Powder Coating Gun: A specific gun that electrostatically charges the powder for even application. Brands like Eastwood and Harbor Freight offer reliable options.
- Powder Coating Oven: A dedicated oven is necessary to cure the coating. Some use standard kitchen ovens, but a convection oven is preferred for a more uniform heat distribution.
- Compressor: A compressor provides the airflow needed to operate the coating gun effectively. Make sure it has adequate pressure capacity.
- Protective Gear: Safety equipment, such as gloves, goggles, and masks, should never be overlooked. Protecting your skin and lungs from powder particles is vital.
- Surface Preparation Tools: Sandblasting or grinding equipment to prepare surfaces ensures better adhesion. Properly cleaning the material will yield a superior finish.
- Powder Coating Materials: A selection of powders in different colors and finishes will allow creative expression.
Step-by-Step Guide for Beginners
For those new to powder coating, following a systematic approach can simplify the process. Here’s a basic step-by-step guideline to get started:
- Choose Your Object: Start with a metal piece to ensure optimal results. Clean and inspect it for any damage.
- Surface Preparation: Clean the surface thoroughly. Remove any rust, dirt, or previous coatings. Sandblasting is the most effective method, yet degreasing might also suffice.
- Set Up Your Workspace: Ensure you have a ventilated area. Gather all tools: your powder coating machine, oven, and protective gear.
- Apply the Powder: Attach your piece to a grounded surface. Using the powder coating gun, evenly coat the surface with thin layers. Try to maintain a consistent distance for even application.
- Cure the Coat: Place the coated item in the preheated oven. Follow the recommended curing temperature and times from your powder's specifications.
- Inspect and Finish: Upon cooling, inspect your project. If satisfied, your DIY powder coated item is ready for use.
- Cleanup: Always clean tools and workspace to maintain a safe environment. Proper storage of powder and equipment is also important for future projects.
By following these steps, you can achieve professional-looking results at home. DIY powder coating opens doors to creativity and can be a cost-effective solution for many applications.
"With the right tools and knowledge, anyone can master the art of powder coating at home."
Professional Powder Coating Services
The realm of powder coating is vast, but when it comes to achieving top-notch finishes, hiring professional powder coating services becomes essential. Not all powder coatings are created equal, and professionals bring an expertise that is vital for ensuring superior quality. They have access to specialized equipment and materials that may not be available for DIY enthusiasts. Their knowledge allows for more consistent application and resulting longevity, which directly influences the aesthetics and durability of the coated product.
With the right service provider, projects can be completed more efficiently. Professional services usually come with a guarantee of the work done, which can be reassuring. This means that any unforeseen issues that arise post-application may be rectified without additional costs to the customer.
Choosing the Right Service Provider
Selecting a suitable service provider for powder coating is a crucial step. Not only does this affect the quality of the finish, but it also can impact the overall cost and timeline of your project. Here are several considerations:
- Experience: Look for providers who have a solid background in powder coating, particularly for the type of material and finish required.
- Portfolio: A well-established service provider should have a portfolio or examples of previous work. This will give insight into their capabilities and styles.
- Reviews and References: Seek past customer reviews and testimonials. Word of mouth can provide invaluable insight about reliability and service quality.
- Certifications: Check if the provider holds relevant certifications or affiliations with industry associations. This can indicate professionalism and commitment to best practices.
"Investing time in selecting the right powder coating service provider can yield substantial returns in quality and durability."
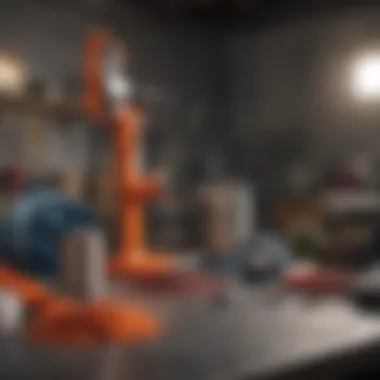
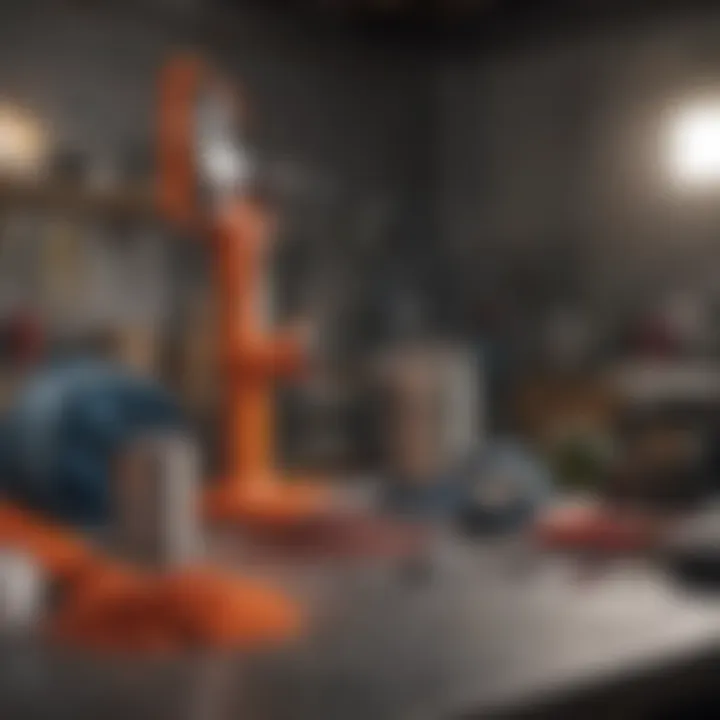
Understanding Pricing Structures
Pricing for professional powder coating services varies significantly based on several factors. Understanding the pricing structure can help you make informed decisions. Key elements to consider include:
- Material Costs: The type of powder used can affect pricing. Specialty powders or custom colors may come at a premium.
- Surface Preparation: The complexity of the surface preparation required can significantly influence cost. More preparation time translates to higher labor costs.
- Batch Size: Many providers have minimum order costs, so combining items for coating may save on expenses.
- Finish Requirements: Specific finish requirements such as texture or gloss level can add to costs, depending on the provider's capabilities.
- Turnaround Time: Rush jobs or expedited services usually incur additional fees.
In summary, assessing potential service providers involves evaluating their experience, examining past work, and understanding their pricing structures. This ensures that your choice aligns with your expectations and budget, maximizing the benefits of professional powder coating.
Common Issues and Troubleshooting
Common issues and troubleshooting play a critical role in understanding powder coating. This section addresses the defects that may occur during the powder coating process and outlines effective preventative measures. Such knowledge helps professionals and hobbyists alike to enhance the overall quality of their coatings and achieve better results. Recognizing and resolving issues early minimizes time and resource wastage, ultimately improving customer satisfaction.
Defects in Powder Coating
Defects in powder coating can hinder the intended aesthetic and functional benefits of the coating. Common defects include:
- Orange Peel: This defect results from an improper application or curing that leads to a textured surface resembling an orange peel.
- Poor Adhesion: Insufficient surface preparation or contamination can cause the powder to peel away easily, reducing durability.
- Color Variations: Inconsistent application can lead to color mismatches, which may be unacceptable for high-end projects.
- Bubbles and Pinholes: These occur due to trapped gases in the powder or from moisture on the substrate.
It is crucial to identify these issues early. Regular inspection of the coating process and maintaining a clean working environment are essential steps to prevent such defects from arising.
Preventative Measures
Preventative measures focus on ensuring a successful powder coating process. Implementing these strategies can lead to the production of high-quality finishes while decreasing the chances of defects:
- Surface Preparation: Properly clean and prepare surfaces by removing any oils, dirt, or rust. Abrasive blasting or chemical cleaning agents can improve surface texture and ensure good adhesion.
- Consistent Application: Use specialized equipment, such as electrostatic spray guns, for even and efficient powder distribution. Adhere to recommended distance and speed during application to avoid uneven coating.
- Controlled Environment: When possible, perform powder coating in a controlled environment where humidity and temperature are regulated. Keeping moisture and airborne particles at bay helps reduce the risk of contamination.
- Regular Equipment Maintenance: Regularly check and clean the powder coating machinery. Worn-out parts can lead to uneven or improper application.
By taking these preventative measures seriously, a smoother and defect-free powder coating experience can be achieved.
"Understanding and troubleshooting common issues is essential for anyone involved in powder coating, regardless of experience level."
Keeping these guidelines in mind allows coaters to not only enhance the quality of their work but also develop a deeper appreciation for the intricacies of powder coating.
Future Trends in Powder Coating
Understanding the future trends in powder coating is essential for both manufacturers and consumers. As industries evolve, the demand for innovative solutions grows. These trends reflect advancements in technology, sustainability practices, and market dynamics. Being aware of these trends allows stakeholders to make informed decisions and adapt to changing demands.
Innovation in Materials and Techniques
The future of powder coating heavily relies on innovative materials and application techniques. Manufacturers are experimenting with new formulations that enhance performance characteristics. For example, environmentally friendly powders that reduce VOC emissions are gaining traction.
New tech in application methods, like ultraviolet curing, is being explored, offering faster processing times and better energy efficiency. Hybrid coatings that combine properties like durability and aesthetic appeal are also becoming more popular. This innovation leads to products that are more adaptable to various applications, from automotive to architectural finishes.
Additionally, the development of smart coatings that provide self-cleaning or anti-graffiti properties is on the rise. These advancements contribute not only to the longevity of finishes but also to increased satisfaction amongst end-users.
Market Growth and Opportunities
The powder coating market is experiencing robust growth. Factors such as increased demand in construction and automotive sectors, as well as the shift towards sustainable practices, are driving this expansion. The market is expected to grow significantly over the next few years, providing opportunities for new businesses and technologies.
The global emphasis on sustainability further boosts this market. More companies are seeking eco-friendly powder coating solutions, which can create a competitive advantage.
"Sustainability is no longer an option for businesses, but a necessity for survival in a competitive market."
Overall, understanding these trends will enable consumers and professionals to embrace new methodologies that enhance product quality and environmental responsibility. Investing in knowledge of these future developments will foster a more sustainable and prosperous industry.
Closure
In wrapping up our exploration of powder coating, it is essential to recognize its significant role in modern manufacturing and crafts. This article has highlighted several core aspects, such as the benefits, application techniques, and the importance of understanding the materials involved. Powder coating excels in delivering superior durability, aesthetic appeal, and environmental advantages.
The processes discussed, including surface preparation, application, and curing, show how precision in these steps leads to the quality of the final product. Furthermore, the methods of choosing the right powder—considering factors like color and finish—directly influence the results one can achieve.
Recap of Key Points
- Definition and History: Powder coating is a versatile finish that provides both functional and decorative properties to various materials. Its evolution has made it a preferred choice across industries.
- Process Overview: Key stages like surface preparation, application, and the curing process are critical to achieving high-quality results. Each step requires attention and proper technique.
- Materials: Different types of powders are available, with options that cater to distinct aesthetic and durability needs.
- Advantages: The advantages of powder coating—such as environmental benefits, cost-effectiveness, and resistance properties—underscores its importance as a go-to finishing method.
- Applications: From industrial to consumer applications, powder coating is widely used, demonstrating its versatility.
- Troubleshooting and Trends: Understanding common issues and staying informed about future trends can enhance one’s approach to powder coating.
Encouragement for Continued Learning
Learning about powder coating is not just about understanding current capabilities. It's an ever-evolving field, with ongoing advancements in materials and techniques. Exploring sources such as Wikipedia or industry blogs can deepen your knowledge. Joining communities on platforms like Reddit or Facebook can also provide valuable insights and support.
Ultimately, whether you are an enthusiast or a professional, continual education in powder coating can lead to improved practices, innovative ideas, and enhanced project outcomes. Embrace the journey of learning, and don’t hesitate to experiment with different techniques and materials. With hands-on experience, you will refine your skills and contribute to this dynamic field.